Eco-friendly UFO High Bay Luminaire, boasting up to 78% energy savings. Tailor illumination with customizable wattage and color temperature options, perfect for warehouses and industrial spaces, helps to optimize efficiency and productivity in your business environment.


;
Eco-friendly UFO High Bay Luminaire, boasting up to 78% energy savings. Tailor illumination with customizable wattage and color temperature options, perfect for warehouses and industrial spaces, helps to optimize efficiency and productivity in your business environment.
DLC Premium listed fixtures, offering wide distribution and 4000K/5000K color temp at 120-347V. Customize with Emergency Battery Backup. Explore mount options, wire guards, and sensors for expanded applications.
Our Vapor Tight luminaires feature corrosion-resistant housing, stainless steel mounting accessories, and waterproof fittings. With up to 84,000 hours of life, versatile voltage options, and DLC Standard and Premium certifications.
Primary Challenges in Industrial Warehouse Lighting
Explore the primary challenges in warehouse lighting and discover LEDVANCE's responsive solutions.
Energy Costs
Traditional options such as incandescent and fluorescent bulbs consume excessive amounts of energy and drive up bills. LEDVANCE offers a warehouse lighting solution powered by LED technology, which not only saves significant energy costs but also reduces greenhouse gas emissions. Upgrading to LED warehouse lighting is a smart investment for cutting costs and environmental impact.
Color Temperature
Warmer light (below 3000K) stimulates the brain to produce more melatonin, the sleep hormone, leading to drowsiness. Conversely, cooler color temperatures (>5000K), akin to daylight, promote alertness and wakefulness. At LEDVANCE, our warehouse lighting options include models with selectable color temperatures of 4000K and 5000K, allowing you to tailor the lighting to enhance productivity based on specific requirements.
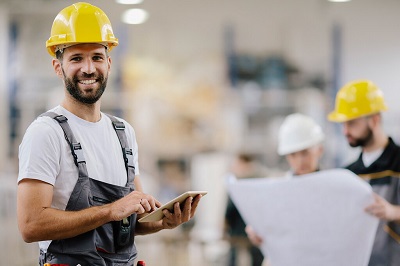
Safety and Compliance
Proper lighting is essential to safeguarding workers and meeting regulatory requirements concerning illumination standards, emergency lighting protocols, and the classification of hazardous areas. With LEDVANCE's industrial warehouse lighting solution, you can ensure a safe and compliant workspace environment.
Design Tips for Industrial Warehouse Lighting
Explore the best solution warehouse lighting.
Design Tips: The structural framework of industrial buildings, especially warehouses, forms interior spaces called “bays”. The selection of general lighting luminaires is based on the height of the bay and should provide more or less uniform illumination of the area:
Low-bay – bottom of the luminaire is <18 ft. off the floor
Medium-bay – bottom of the luminaire is 18-25 ft. off the floor
High-bay – bottom of the luminaire is >25 ft. off the floor
Since the majority of tasks occur in the vertical plane, it should provide 20-30-foot candles of uniform illumination on the vertical surface of goods stored on the racks.
Note: The glare reflection can hinder readability and scanning accuracy, it may cause issues for navigating aisles and reading pick tickets for forklift operators. Therefore, it's essential to minimize glare from light sources.
Additionally, it's important to shield light sources, especially HID, to prevent disability glare when looking up at the tops of racks. Indirect luminaires, paired with reflective ceilings, offer optimal visual comfort, particularly when using display screens at workstations, handheld terminals, and forklifts.
Warehouse Luminaire Considerations:
-
For aisles 15 feet and above, classic high-bay HID luminaires are suitable. These luminaires should be spaced closely to eliminate dark areas between them.
-
Increase spacing for low-bay or aisle-lighting luminaires with asymmetric light distribution.
-
Highly efficient T8 and T5 HO fluorescent luminaires are suitable for mounting heights up to 30 feet. They can be installed either in continuous rows along an aisle or individually mounted, with options including reflector, lensed, or open designs.
-
To optimize energy usage in warehouse spaces that are only accessed intermittently, consider installing motion sensors and control devices. These can interface with HID and fluorescent multilevel ballasts to automatically adjust light levels when the space is unoccupied by personnel or equipment.