The Occupational Safety and Health Administration (OSHA) has specific workplace lighting standards. These standards protect workers from the potential hazards of poor lighting, including eye strain, fatigue, and accidents.
OSHA's standards for lighting are based on the recommendations of the Illuminating Engineering Society of North America (IESNA), a professional organization that develops standards for lighting design and installation.
In brief,
OSHA standard for lighting requires employers to provide adequate lighting in all work areas. Read on to get the detailed info about OSHA.
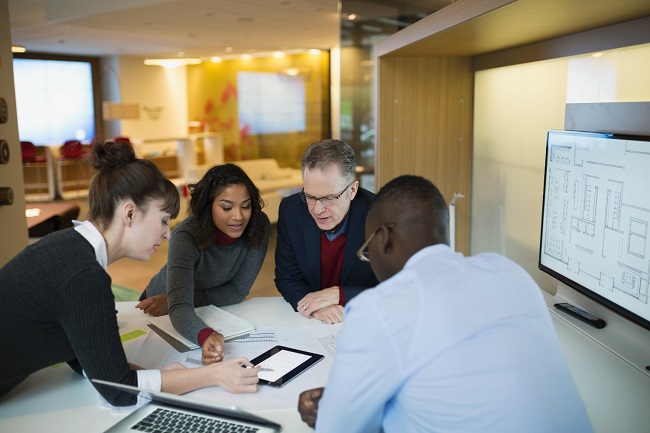
Lighting Requirements Per OSHA
There are specific OSHA requirements for lighting in different types of workplaces. For example, the standards for general office lighting, factory lighting, and mining lighting are different.
OSHA requires employers to maintain a certain illumination level in all work areas. This level is known as the minimum light intensity measured in foot-candles. Foot-candles are a unit of measurement that indicates the amount of light falling on a given surface. In this part, we will show you these concepts one by one.
Foot-candle
OSHA standard for lighting uses foot-candles to measure lighting intensity. One foot-candle is equivalent to the amount of light cast on a surface by one candle at one foot.
Though foot-candles are not used frequently now, they are still used in some industries. The modern unit of measure for light intensity is Lux, a metric unit of measurement equal to one lumen per square meter. It is a more accurate way to measure light intensity and the standard unit of measure used in the lighting industry.
OSHA requires a minimum of 30 foot-candles of light on work surfaces.
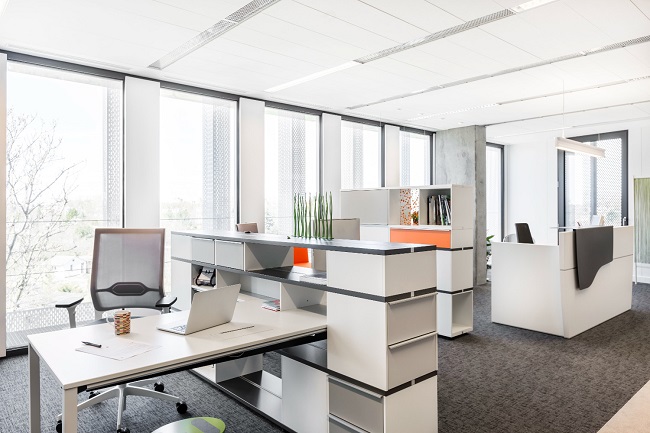
OSHA requires a minimum of 5 foot-candles of light on work surfaces and 10 foot-candles for general construction plants and shops.
OSHA standard for lighting requires a minimum of 5 foot-candles of light, 10 foot-candles for tunnel and shaft heading
OSHA Compliance Benefits
Following OSHA's standards for lighting can provide several benefits for employers, including:
-
Reduced risk of accidents and injuries
-
Increased productivity
-
Reduced eye strain and fatigue
-
Improved morale
-
Reduced costs associated with lighting repairs and replacements
In addition to the benefits to workers, complying with OSHA lighting standards can also have a positive impact on an employer's bottom line. Proper lighting can improve productivity by making it easier for employees to see what they are doing. Studies have shown that increasing light levels can lead to significant increases in productivity. In addition, better lighting can also reduce energy costs by reducing the need for artificial lighting.
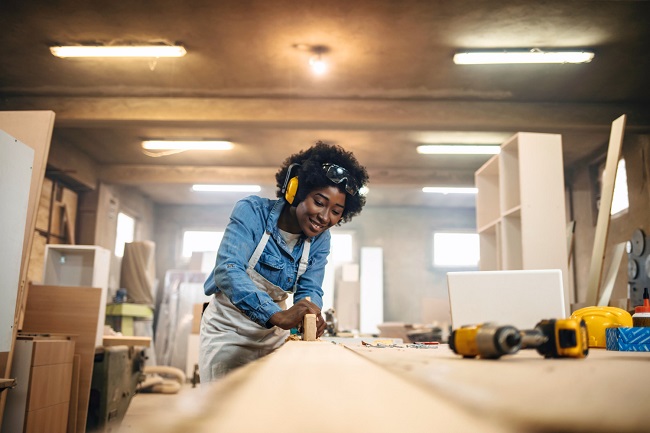
Office Space Lighting Level Recommendations By OSHA
-
Glare from lights and windows shouldn't be reflected on the computer screen
-
OSHA standard for lighting suggests that workplaces use a combination of natural and artificial light and that windows be placed so that workers are not exposed to direct sunlight.
-
According to OSHA, task lighting should be used to supplement the general lighting in an office space. Desk lamps or other task lights can help reduce eye strain and fatigue.
-
Rows of lights should be placed parallel to the line of sight.
-
Adjustable light levels are recommended so that workers can perform different tasks and control the amount of light they expose.
Generalized Workspace Lighting Standards
According to the National Institute of Occupational Safety and Health (NIOSH), office workers spend an average of 7.5 hours per day in front of computer screens. Poor lighting can lead to several problems for these workers, including eye strain, headaches, and fatigue.
To ensure that office workers have adequate lighting, OSHA has established generalized workspace lighting standards. These standards require that:
-
First aid stations, infirmaries, and office workspaces should be illuminated to a minimum of at least 30fc or 320 lux.
-
Machine shops, carpenter shops, warehouses, and plants should be illuminated to a minimum of at least 10fc or 110 lux.
-
Shipyard drinking, eating areas, showers, and restrooms should be illuminated to a minimum of10fc or 110 lux.
For more information, check the
OSHA website.
OSHA Fixture Requirements
OSHA also has specific requirements for the fixtures that are used in workplaces. These requirements are listed in standard
1926.405.
-
Fixtures shouldn't have any live parts exposed to employee contact.
-
Fixture wire parameters should align with environmental conditions, as well as with voltage.
-
Fixtures should be securely mounted.
-
Fixtures must be protected with a cover.
-
Fixtures weighing more than 6 pounds shouldn't be supported by the lampholder's screw shell.
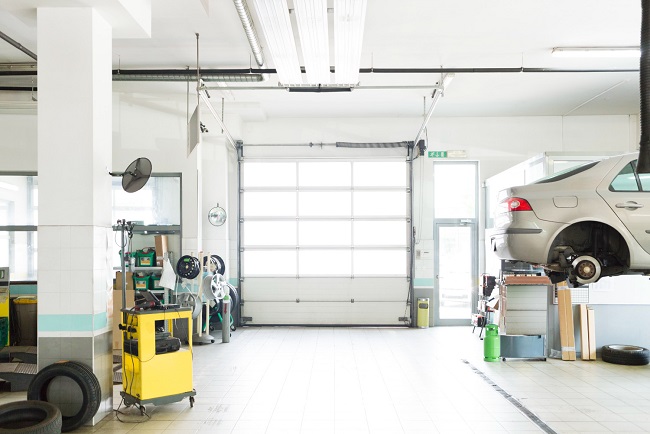
Bottom Line
OSHA has several standards for workplace lighting, both general and specific to certain types of workplaces or tasks. These standards provide many benefits for employers, including reducing the risk of accidents and injuries, increasing productivity, and reducing costs associated with lighting repairs and replacements. In addition, complying with OSHA lighting standards can also have a positive impact on an employer's bottom line.
Proper lighting can improve productivity by making it easier for employees to see what they are doing. Studies have shown that increasing light levels can lead to significant increases in productivity. In addition, better lighting can also reduce energy costs by reducing the need for artificial lighting. Following these standards can help create a safer and more productive workplace for employees.